Boost Equipment Longevity
Enhance Operational Efficiency
Reduce Maintenance Costs
Resilience in the Recycling Process
Recycling is a high-demand, abrasive industry. With 300 Below’s cryogenic
treatment, ensure your equipment can withstand the challenges and deliver
consistent high performance.
Materials Impacted
At 300 Below, we understand the unique challenges faced by the recycling industry. Our
cryogenic treatment refines the molecular structure of your equipment parts, improving
their durability and performance, and helping you achieve better results.
Improve efficiency and reduce costs with our cryogenic treatment. Please contact us for a personalized quote.
At 300 Below, we understand the diverse needs of the recycling industry, and our cryogenic treatment process caters to a wide array of applications within this sector. Here’s how our technology can be utilized

Extrusion Equipment
Enhance the reliability and performance of extruders, extrusion screws, and dies, reducing wear and tear, improving ease of cleaning, and minimizing downtime for changeouts and changeovers.

Material Handling
Increase the efficiency of material air handling processes and improve the longevity and reliability of wear plates, all while ensuring smoother operations.

Pelletizing, Pulverizing, and Grinding
Experience less frequent replacements of pelletizer, pulverizer, and grinder components, including blades and discs. Cryogenic treatment can augment their operational performance, increasing productivity.

Gearboxes and Bearings
Improve the longevity and reliability of gearboxes and bearings, key components that often bear the brunt of mechanical stress in recycling operations.

Granulator Blades and Barrel Sections
Extend the reliability of your granulator blades and barrel sections. Our cryogenic treatment refines their structural integrity, reducing the frequency of maintenance.

Shearing and Cutting Equipment
Boost the performance and durability of shears, nipper blades, and other cutting equipment. Cryogenic treatment can maintain blade sharpness for a longer duration, optimizing cutting processes.

Classifying Equipment
Enhance the performance and longevity of classifiers, critical for maintaining high-quality recycling processes.
Our cryogenic treatment is designed to help recyclers achieve operational excellence, supporting you to meet your target numbers, stay within budgets, secure more contracts, and gain respect within the recycling community. With 300 Below, transform the way your recycling operations run, from the ground up.
Our Process is simple
Make your metal parts better with cryogenic processing for longer lasting, wear-resistant equipment.
Step 1
Identify at-risk metals
Step 2
Upgrade your parts with our process
Step 3
Perform with confidence
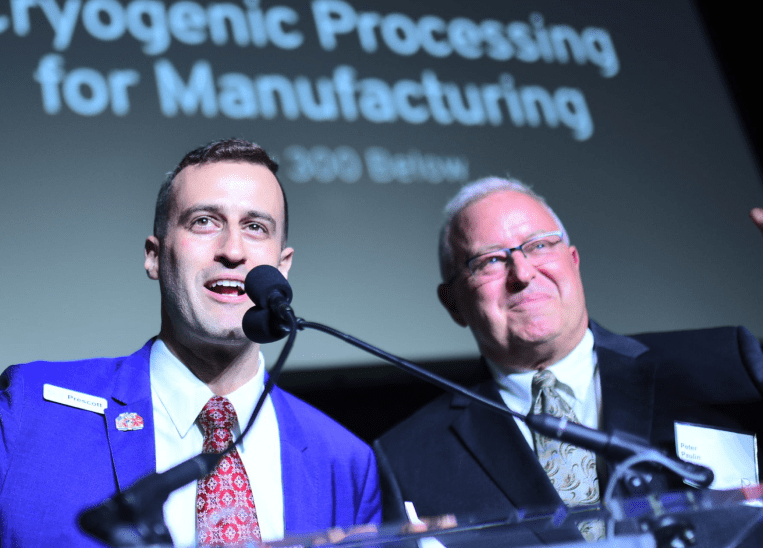
Our Story
At 300 Below, we recognize the consistent efforts of recyclers who continuously push the boundaries of technology to make their operations more reliable. Our cryogenic process has been fine-tuned to cater to the high standards of the recycling industry, focusing on improving the reliability of critical recycling equipment, the key to more efficient, cost-effective operations. Read more…
“Maximize Your Recycling Capabilities”
Download our Cryogenic Processing Overview brochure to explore how our technology can revolutionize your recycling operations.
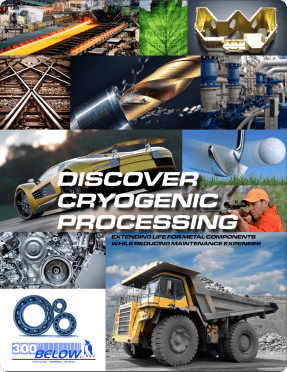
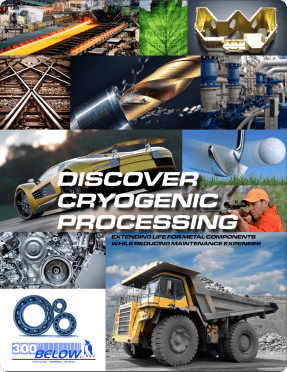
“Maximize Your Recycling Capabilities”
Download our Cryogenic Processing Overview brochure to explore how our technology can revolutionize your recycling operations.