Prolong Your Equipment Lifespan
Minimize Downtime
Boost Operational Efficiency
The Power to Move Mountains
Don’t let equipment failure slow down your earthmoving operations. Embrace the
improved durability and performance offered by 300 Below’s cryogenic treatment.
Prolong Your Equipment Lifespan
Our cryogenic treatment process refines the molecular structure of your earthmoving and cold-milling equipment, extending their operational lifespan and lessening the frequency of replacements. This saves you money in long-term capital expenses.
Minimize Downtime
With cryogenic processing, your equipment’s performance improves significantly, leading to fewer equipment failures. Less downtime means smoother, uninterrupted operations, helping you hit your productivity goals.

Boost Operational Efficiency
Our cryogenic treatment isn’t merely a band-aid solution, but a transformational process that increases wear resistance, reduces maintenance intervals, and ultimately saves costs—elevating your operations’ efficiency.
Materials Impacted
We understand the crucial role of efficient and reliable equipment in earthmoving
operations. That’s why we offer our pioneering cryogenic treatment to refine the molecular
structure of your equipment parts, maximizing their potential and durability.
Our cryogenic treatment services are cost-effective and offer a high return on investment by enhancing your equipment’s lifespan and performance. Please contact us for a personalized quote.
In the world of road construction and earthmoving, every component plays a vital role in ensuring smooth operations. Our cryogenic process has transformative implications for a broad range of equipment, including but not limited to

Pinner Bits
Enhance the longevity and functionality of your pinner bits, helping them withstand wear and tear and perform optimally even under extreme conditions.
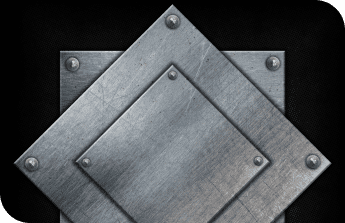
Wear Plates
Increase the wear resistance of your wear plates, thereby reducing the frequency of replacements and contributing to the overall operational efficiency.

Screens
Maintain the resilience of your screens and sifters, ensuring they perform with unwavering accuracy and endurance.

Air Handlers
Protect your material air handlers from premature wear, enhancing their durability and facilitating smooth material handling.

Coal Rotors
Boost the lifespan of your coal rotors, improving their resistance to operational stresses and increasing their overall efficiency.

Milling Bits
Maximize the performance of your milling bits, ensuring they remain sharp and effective even under constant use.

Saw Blades
Improve the longevity and cutting performance of your saw blades, maintaining their sharpness and enhancing overall productivity.
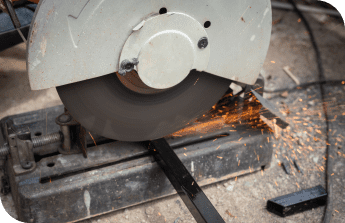
Cutters and Cutting Equipment
Enhance the durability of your cutting equipment, ensuring they perform at peak levels for prolonged periods, leading to improved operational efficiency.

Classifiers
Safeguard your classifiers from wear and tear, ensuring they consistently provide accurate sifting and classification of materials.
When each component of your earthmoving operations is functioning at its best, your overall productivity goes up, downtime will decrease, and deadlines will be met with greater ease. Our cryogenic process is designed to enhance every aspect of your operations, propelling your company towards increased efficiency, profitability, and growth.
Our Process is simple
Make your metal parts better with cryogenic processing for longer lasting, wear-resistant equipment.
Step 1
Identify at-risk metals
Step 2
Upgrade your parts with our process
Step 3
Perform with confidence
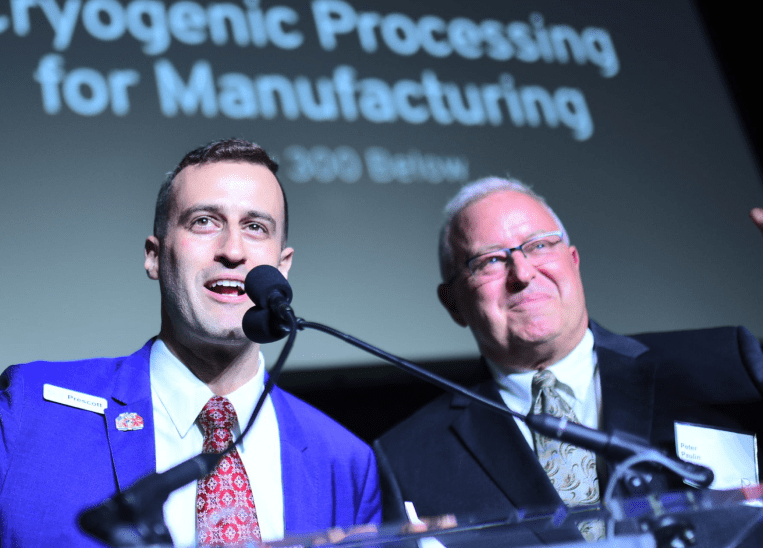
Our Story
As a fleet manager, reliability engineer, or operations manager, you know the importance of efficient and reliable equipment in road construction and earthmoving operations. It’s the lifeblood of your productivity and the heart of your business’s success. Read more…
Enhance Your Earthmoving Capabilities”
Download our Cryogenic Processing Overview brochure to learn more about how our technology can boost your earthmoving operations.
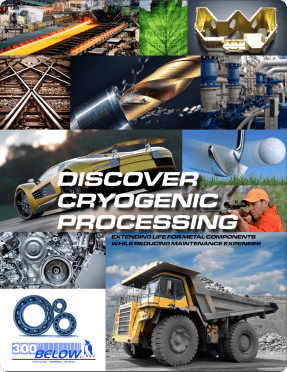
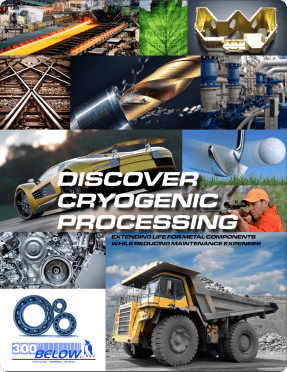
Enhance Your Earthmoving Capabilities”
Download our Cryogenic Processing Overview brochure to learn more about how our technology can boost your earthmoving operations.