Enhance Firearm
Accuracy and Lifespan
Boost Durability of
Armored Vehicles
Achieve Improved
Metal Stability
Exceptional Performance, Maximum Operational Readiness
In the defense arena, the stakes are high, and there is no room for equipment
failure. With 300 Below’s cryogenic treatment, ensure your firearms and armored
vehicles are at their optimal performance and ready for any mission.
Enhance Firearm Accuracy and Lifespan
Our cryogenic treatment significantly improves the accuracy and potentially triples the lifespan of firearm barrels. Experience a marked performance improvement that gives your operations a distinct edge.
Boost Durability of Armored Vehicles
Increase the service life of critical components such as brake rotors in armored vehicles like HMMWV and JLTV. Benefit from enhanced durability under extreme conditions, reducing maintenance needs and costs.
Achieve Improved Metal Stability
Our cryogenic process enhances the molecular structure of metals, leading to improved stability and precision in all your defense applications, optimizing your operations.
Materials Impacted
We at 300 Below understand the crucial role that durability and precision play in defense
operations. Our cryogenic treatment process refines the structure of metals in firearms and
armored vehicles, contributing to enhanced performance and resilience in high-stake missions.
Invest in exceptional performance and longevity for your defense metals with our cryogenic treatment. Please contact us for a personalized quote.
Revolutionizing Defense Capabilities
From precision-enhanced firearms to robust armored vehicles, our cryogenic process can bring transformative improvements to a wide range of defense applications. Experience enhanced performance and durability of at-risk metals, contributing to mission success and operational readiness.
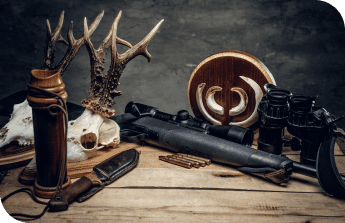
Firearm Barrels
Our cryogenic treatment potentially triples the lifespan of gun barrels and enhances their accuracy.

Brake Rotors
Improve the durability of brake rotors in armored vehicles, and reduce maintenance costs.

Transmission Components
Enhance the performance of vehicle transmissions, leading to smoother operation and extended component life.
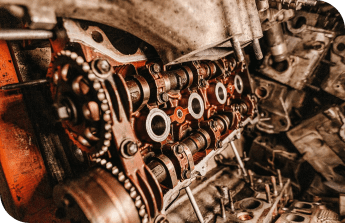
Engine Parts
Improve the reliability of military vehicle engine parts, ensuring smooth operations under the toughest conditions.
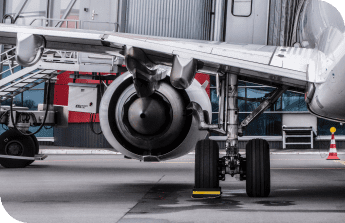
Aircraft Landing Gear
Strengthen critical components of aircraft landing gear, enabling them to withstand high-stress conditions.

Naval Propeller Shafts
Increase the lifespan of naval propeller shafts, leading to a reduction in maintenance and replacement costs.
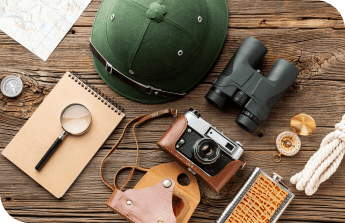
Military Tools & Equipment
Improve the resilience and lifespan of field tools, ensuring reliable performance even in harsh conditions.
Tank Tracks & Pads
Extend the lifespan of tank tracks and pads (when using polymer materials), which helps reduce the frequency of replacements and downtime.

Drone Components
Improve visual acuity and reliability in military drones, among optical housings and mounting hardware, to improve performance, durability, and stabilization.

Weapon Mounts and Attachments
Increase the reliability and lifespan of weapon mounts and attachments.

Nuclear Submarine Components
Enhance the longevity and reliability of vital nuclear submarine components, enabling smoother operations under extreme conditions.
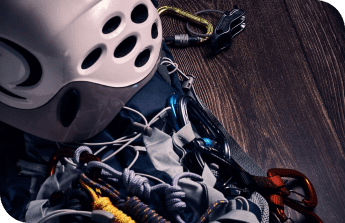
Parachute Harnesses
Increase the durability and lifespan of parachute harness components, ensuring optimal performance and safety.

Military-grade Electronics
Extend the lifespan of military-grade electronics by enhancing the reliability of their key components and housings.
With our innovative cryogenic treatment, you can enhance a broad array of military applications. You will gain superior reliability, reduced maintenance and downtime, and significant cost savings over time. Experience the edge that 300 Below’s cryogenic treatment provides in military operations.
Our Process is simple
Make your metal parts better with cryogenic processing for longer lasting, wear-resistant equipment.
Identify at-risk
metals
Step 1
Upgrade your parts
with our process
Step 2
Perform with
confidence
Step 3
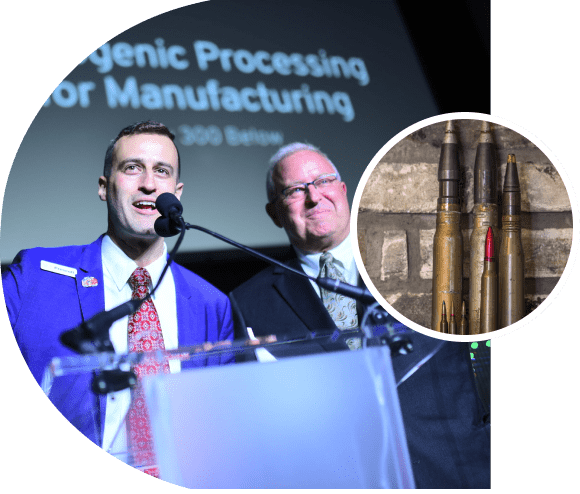
Our Story
Navigating the demanding environment of military operations calls for reliability, performance, and the most stringent standards of precision. At 300 Below, we understand this deeply. Our cryogenic treatment process helps ensure that your equipment is not just more durable, but more reliable, allowing for less downtime and fewer failures.
Read more…
“Maximize Your Defense Capabilities”
Download our Cryogenic Processing Overview brochure to explore how our technology can revolutionize your defense operations.
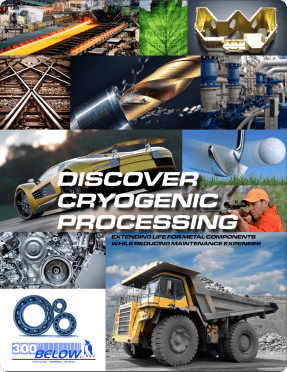
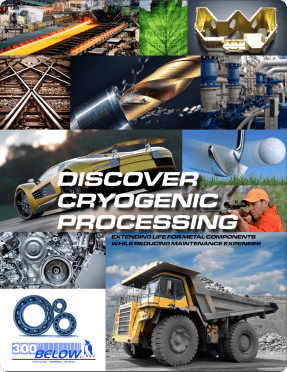
“Maximize Your Defense Capabilities”
Download our Cryogenic Processing Overview brochure to explore how our technology can revolutionize your defense operations.